If you draw often (like me) you will be confronted by the amount of used paper you have at home. Now I do reuse it, just by flipping it over, or folding large sheets into smaller booklets. But when all sides are used, and none are particularly good, what do you do with it?
Each page is actually a store of your time. Right? Some pages only contain a gestural pose of maybe one of two minutes. Other pages may have twenty minutes of your life etched on them. So a single drawing session is approximately two hours manifest as fifteen pages. I draw at least once a week, so in a single year the pile stands 780 pages high.
Needless to say, I have a huge amount of used paper. To add insult to injury, I recently decided to learn watercolour. And so I have another less huge pile of really rubbish paintings, on really good paper. Good paper costs, well even mediocre paper costs, and I am loath to chuck it in the bin. BUT the day comes when you take yourself by the scruff of your own collar, and … (gasp) spring clean!
A few months ago I was doing exactly that when the idea dawned. I need to learn how to make paper. That is the ultimate commitment in recycling. Right? I am a fan of recycling. But the bigger question is: am I a fan of the effort of recycling? I decided to go all in, and put myself on trial, and this article is about that, but mostly it is how you can do it for yourself.
You will need to have some stuff to recycle hours of drawing into sheets of handmade paper. Luckily I already had almost everything at home. Nevertheless I have snooped online and made a list of everything, and its price. There is nothing like numbers of pennies to put the reality of an idea into perspective.
Summary of the process
The process of making paper is actually really boring. It is very repetitive, and there is a fair bit of waiting to be done. The preperation is a bit tricky, and sometimes frustrating, for example how much pulp is needed for a decent page.
In a nutshell this is what needs doing: You judge your work, shred the rubbish, soak the hay of paper, then you liquidise that into a pulp. You take that slimy goop and bathe it, then you dip a screen into the milky water, scoop it up and let it drain a bit. The pulp is then transferred onto a linen sheet, for drying, and you repeat the process until all the goop is gone. Afterwards you hang the linen to dry and return, the next day, when it is done. The satisfying part is peeling the new page off the linen sheet.
The resurrected page is lovely. It has an obvious rough side, and smooth side. The colour is off white, and if you examine it carefully you will notice blemishes, little flakes of its former pigments. This paper has the soul of the work that came before, embedded in its fibre. You may even find yourself reluctant to draw on it, for now it represents the time of your labour, each page a mark of effort, plus the history of all your drawing sessions before that. Perhaps I grew sentimental in my later years.
Now your next drawing on this new hand made page may very well be rubbish too. But you will smile because you know you are fully sustainable. Paper is not a thing you will ever worry about.
Materials & shopping list
Everything you need is listed below. The links go to amazon because I have an Amazon affiliate account. Every click I get, motivates me to do more of these kinds of articles. One day I will have accumulated enough clicks to purchase a pencil sharpener. (No but seriously, writing these articles is actually a lot of work). I should also mention that you could probably find similar things at your local pound store, or nearby mall or mega hardware depo. I am lazy. I have no car. I like to buy the stuff that comes to me.
Required:
- Scrap paper (newspaper, printer paper, junk mail, etc.)
- Wood frames 2 x 13.95 (A3 approx) I used 2 to make both a frame and deckle
- Fly screen (or net curtain, or piece of tule) 6.98
- Linen sheet (or two) for drying goop 6.99
- Liquidiser (or food blender) 24.99
- A large dipping tray (to fit the wood frame) 14.99
Optional (but recommended)
- A stapler (to attach the netting to the frame) 5.19
- Bucket (without a hole, dear Liza) 3.99
- Sieve (if you want to rinse the pulp of old pigment) 3.99
- Ladle (to get consistent density per page, aka paper weight) 3.99
- Paper shredder (scissors and blisters OR paper shredder) 28.04
Step-by-step guide
- Prepare the Paper Pulp:
- Tear the scrap paper into small pieces and soak them in water overnight or for several hours until they become soft. If you have a shredder, use that.
- After soaking, drain excess water and put the paper into a blender or food processor. Add water to cover the paper, then blend until you have a smooth pulp.
- You may want to rinse the pulp again, if the water is heavily tinted.
- Create a Papermaking Mould:
- Construct a wooden frame with a fine mesh screen or use an old picture frame and staple a fine mesh screen to it. This will be your papermaking mould.
- Make sure the frame is slightly larger than the size of paper you want to create, and small enough to fit into the basin you will use.
- (Frame and Deckle) A frame is described above, it has a net mesh covering it. A deckle is a frame alone. It is used to ensure the pulp lies neatly within the area of the frame. (See the images for a better understanding)
- Prepare Your Workspace:
- Lay down towels or plastic sheeting to protect your work surface.
- Forming the Paper:
- Fill a basin or shallow container with water.
- Place your papermaking mould into the basin, ensuring it's submerged in water.
- Stir your paper pulp mixture and pour it into the basin. Add any optional decorative elements at this stage if desired.
- Gently agitate the pulp mixture with your hands to distribute it evenly across the surface of the mould.
- Lifting the Paper:
- Lift the mould slowly and evenly out of the water, allowing the water to drain through the mesh screen.
- Gently shake the mould to distribute the pulp evenly and form a uniform layer on the screen.
- Pressing and Drying:
- Place a sponge on top of the pulp-covered screen to absorb excess water.
- Place another piece of mesh or cloth over the pulp.
- Use a rolling pin or flat board to press down on the cloth, squeezing out more water and compressing the pulp into a cohesive sheet of paper.
- Remove the top cloth and carefully peel the newly formed sheet of paper off the mesh screen.
- Lay the sheet flat on a clean towel to dry.
- Repeat the process to make more sheets of paper.
- Drying and Finishing:
- Allow the paper to air dry, which may take 24-48 hours depending on the thickness of the paper and humidity levels.
- Once dry, gently peel the paper off the towel and smooth out any wrinkles with your hands or by placing it between heavy books.
- Your handmade paper is now ready to use for writing, drawing, or crafting!
Conclusion
Sounds like a lot to do right? Well it is. There is a lot to do. To give you a bearing on my time investment. I have a shredder and gathered a bin bag of sliced paper. I met up with a friend who has a studio workshop, and we spent 3 hours one Sunday going through the steps. The first hour we made the frames (two) liquidised the paper mush, and when the day was done we left the studio with XXX A3 pages drying. Of that original bin bag, we only managed to use one third.
I will update this post again, when I have had some time to draw on the paper. I am curious to see how it copes with different mediums: watercolour, charcoal and ink are my go to favourites. I will let you know honestly what hand made paper is really like.
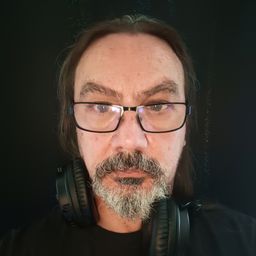